Jungwon National Research Institute of Cultural Heritage
KIM Sukyoung
To restore the step-by-step smelting-hammering-casting iron production process, this project is centered on three methodologies, which are academic research on steel relics, steel technology restoration experiments, and natural scientific analysis.
Recreating Ancient Blacksmithing Techniques through Scientific Methods
The Jungwon National Research Institute of Cultural Heritage embarked on a project to replicate a Baekje iron bar(a 30-centimeter -long, 4-centimeter-wide, and 1.5-centi- meter-thick iron lump weighing 1.2 to 1.3kg) discovered at Tangeumdae Fortress, as well as a sword with ring pommel unearthed from Geumneung-dong, Chungju. To achieve this, we conducted a blacksmithing experiment that involved recreating the original artifact through the application of authentic iron manufacturing techniques, using iron obtained from the smelting of iron ore. The re-creation process employed 78.33kg of bloomery iron, produced during the 7th experiment conducted by the Jungwon National Research Institute of Cultural Heritage. Bloomery iron, due to its low carbon content, lends itself to forging, allowing physical reshaping through plasticity.
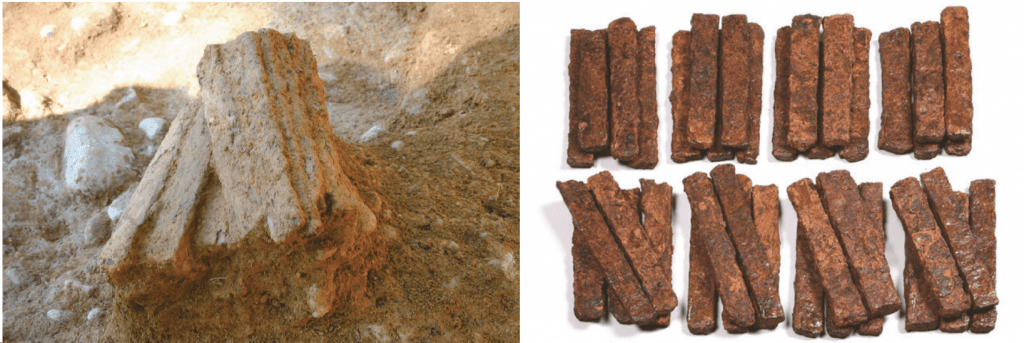
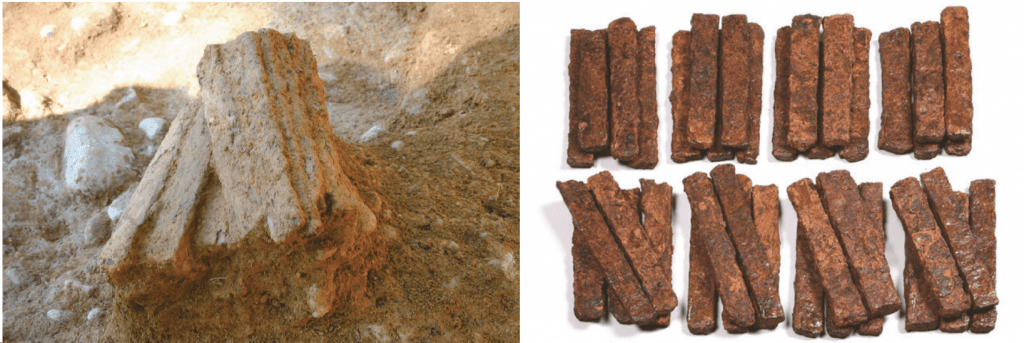
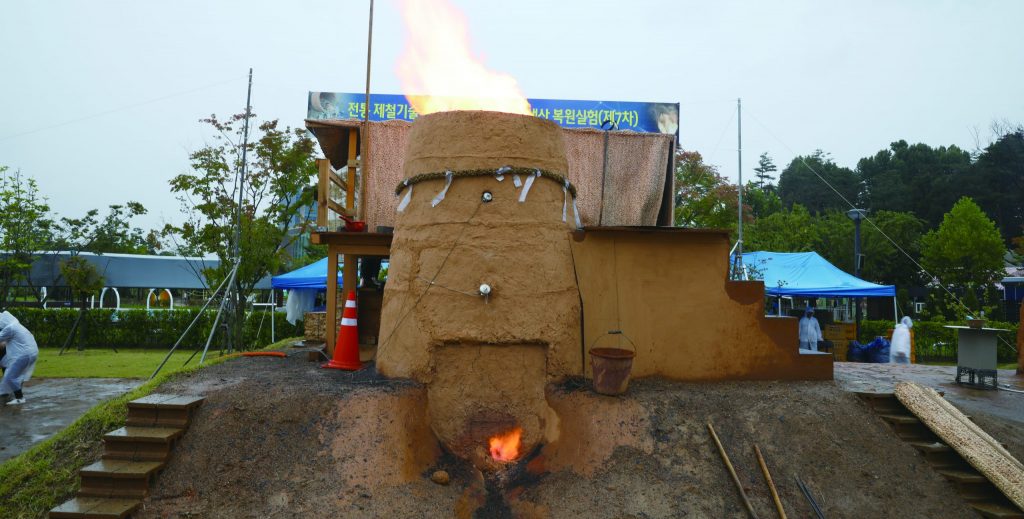
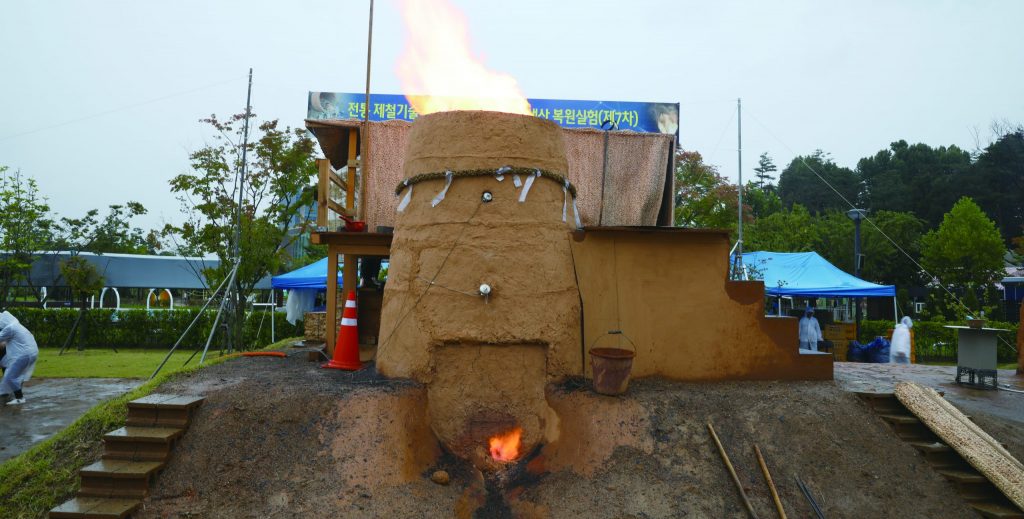
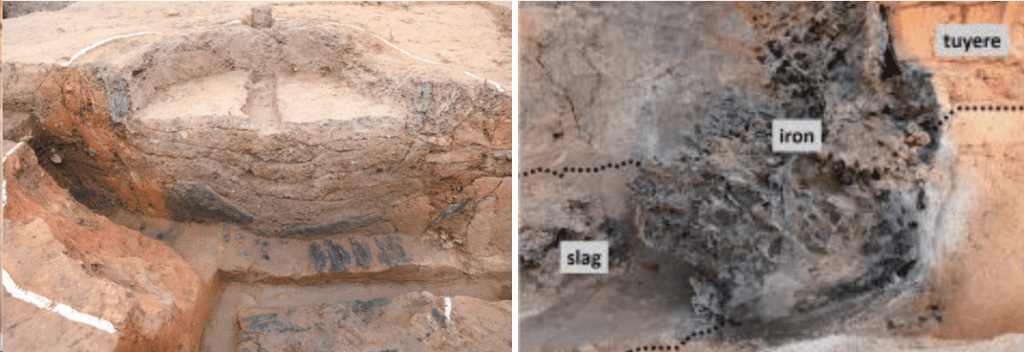
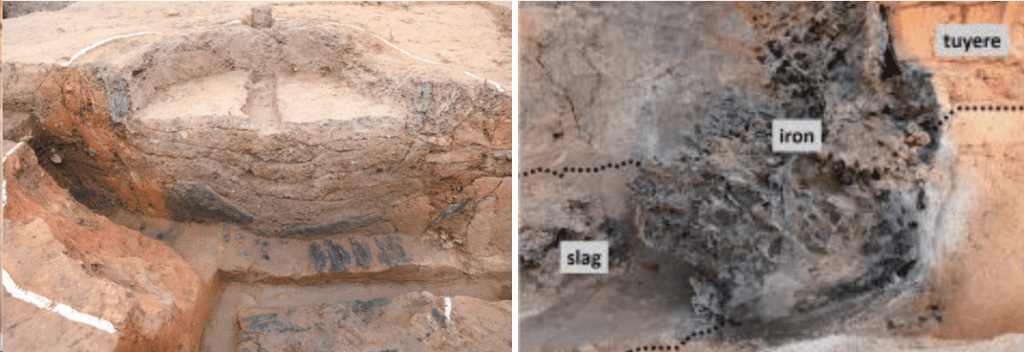
Cutting section after smelting(right)\
Breaking Down the Process Into Refining, Forging, and Molding Stages
Through our experiments, we divided the blacksmithing process into three stages. The first stage is the refining process that involves removing impurities from the iron ingot through dividing and pressing techniques, thereby creating a stackable plate. The forging process ensues, in which the stacked lump is transformed into a lump to enhance its physical properties and form an iron bar through forge welding. This stage resulted in the production of 11 iron bars resembling those found at Tangeumdae Fortress. The final stage, molding, encompasses shaping, cutting, heat treatment, and polishing. By replicating the three-step process, we successfully recreated the Sword with Ring Pommel using a reproduction of an iron ingot.
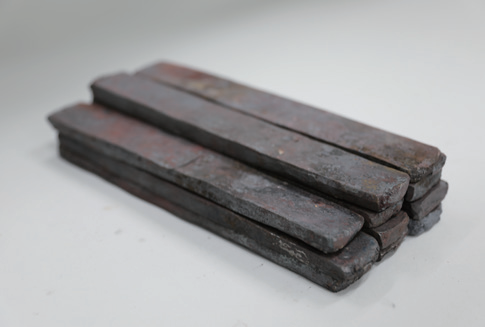
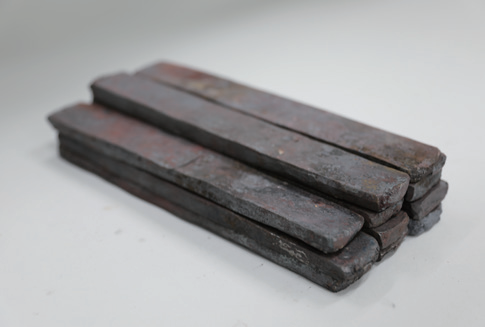
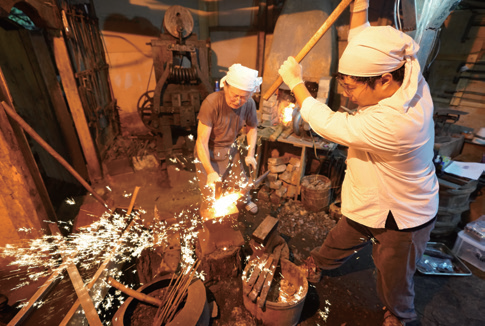
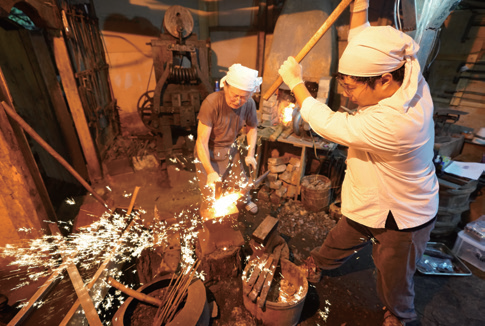
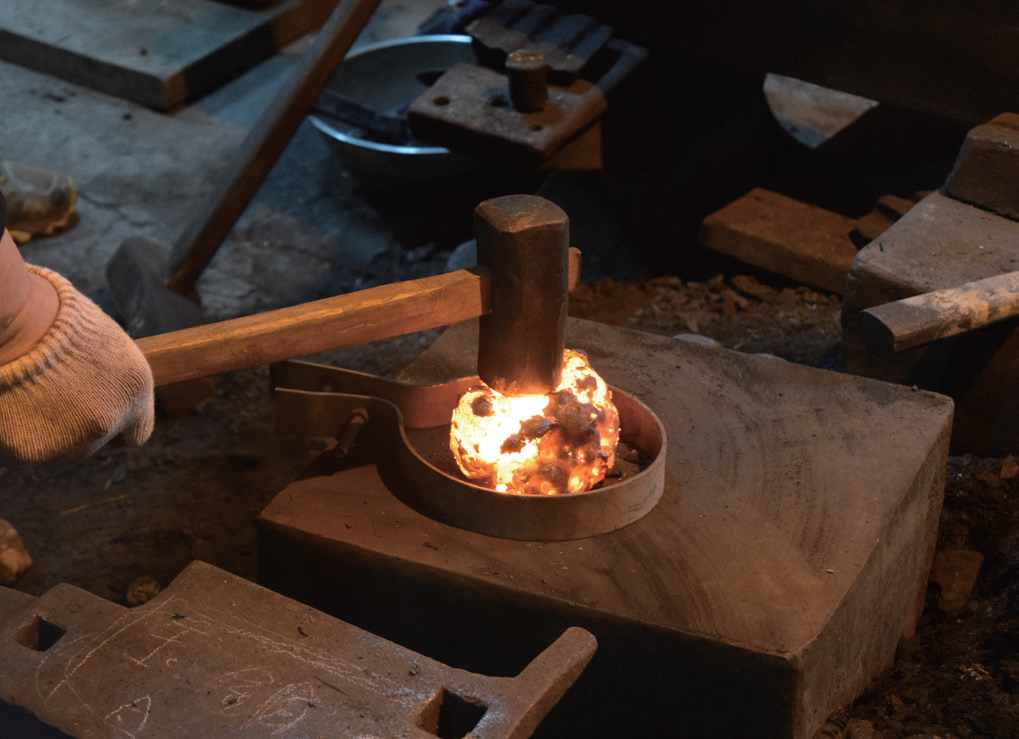
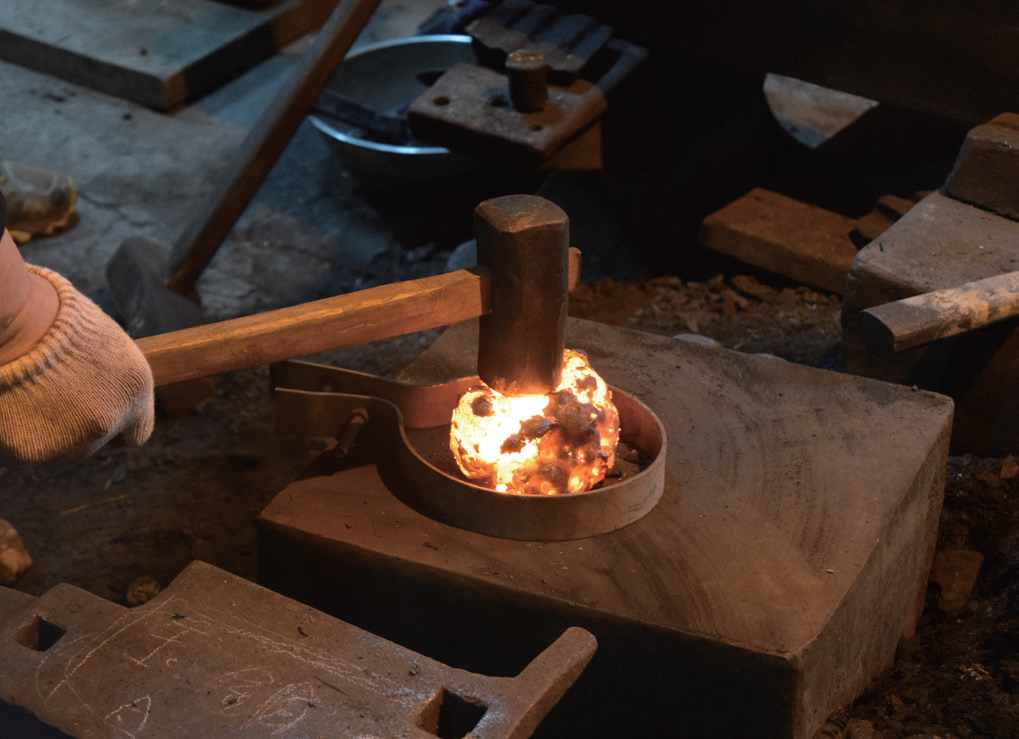
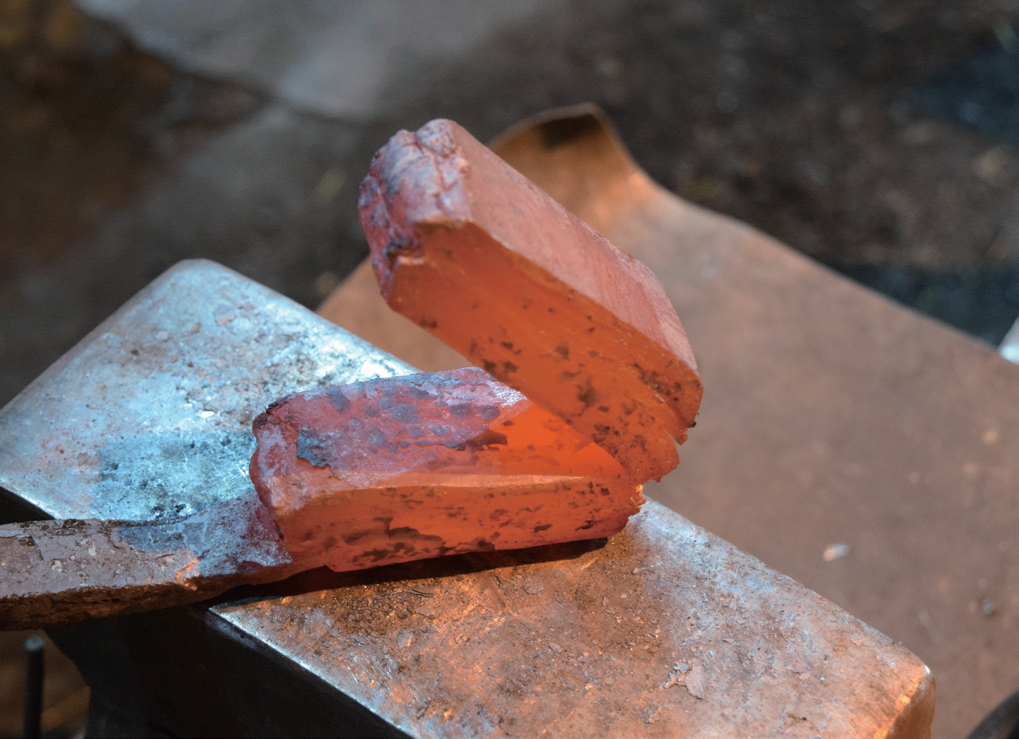
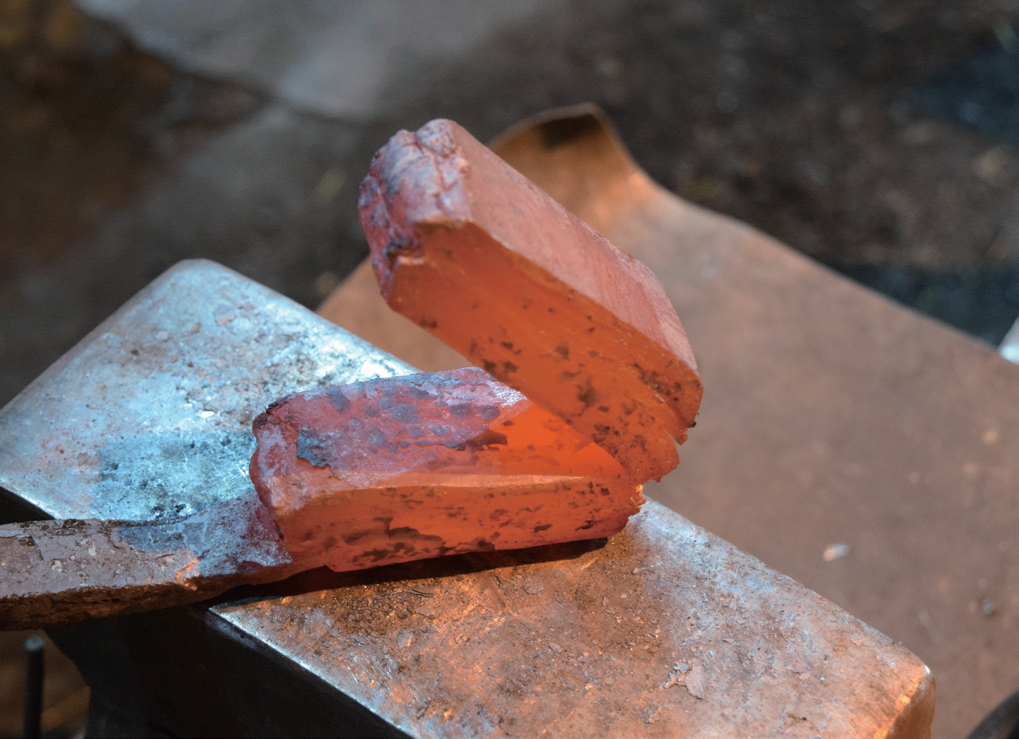
Weight and recovery rate by process
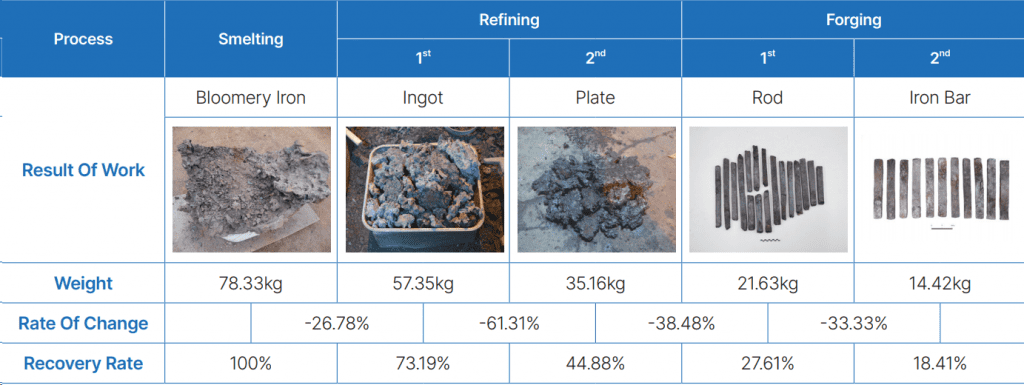
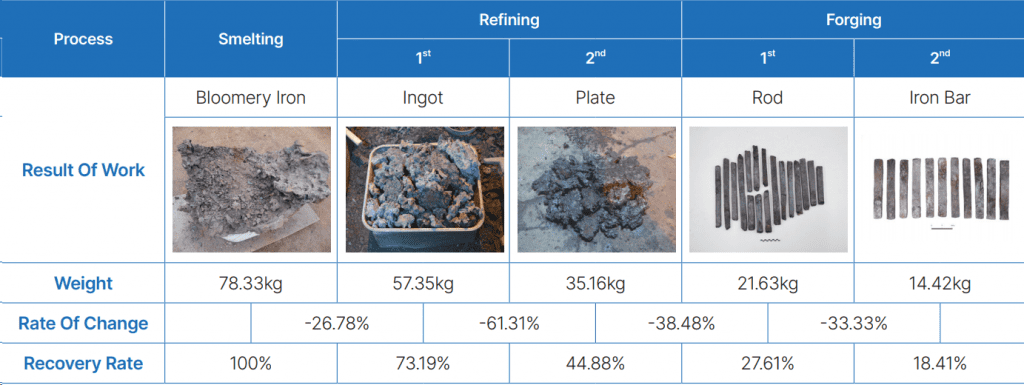
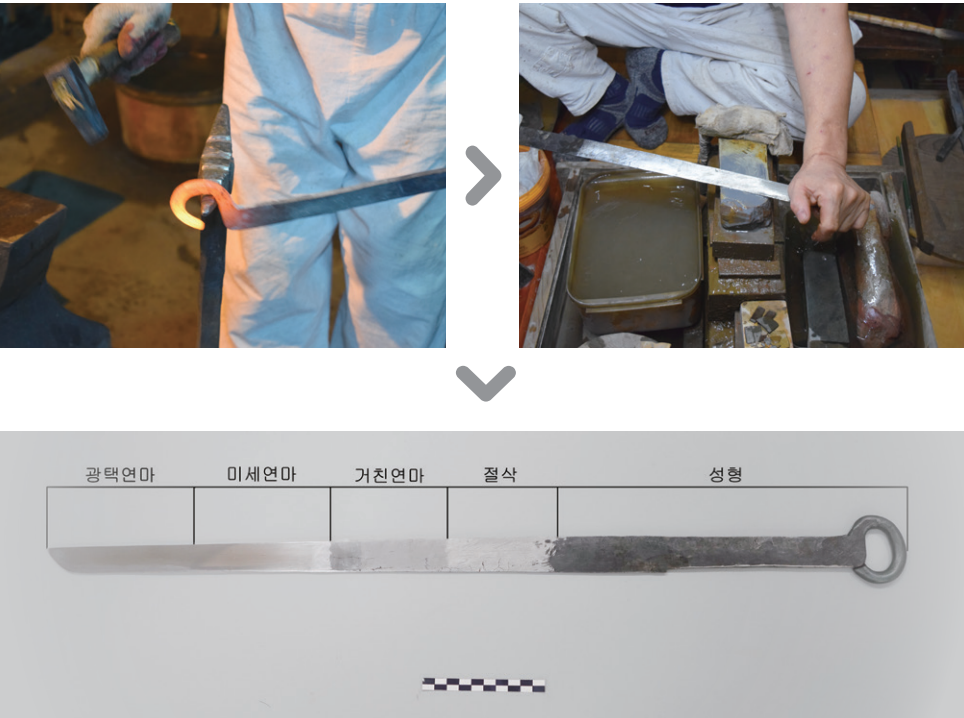
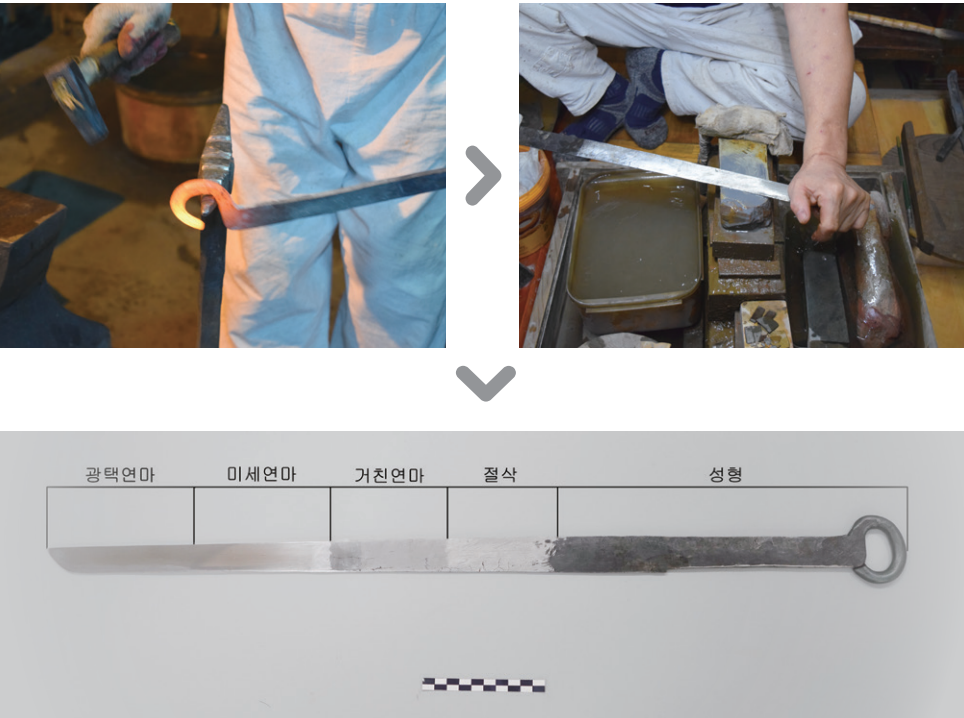
Outcome of the Experiment and Analysis
A total of 14.42kg(18.41%) was recovered from the 78.33kg bloomery iron utilized for the creation of iron bars. The analysis revealed the presence of fayalite(Fe2SiO4) in the initial refining slag. As the refining-to-forging progression unfolded, the thickness decreased and the steel material’s surface became smoother. This transition saw the disappearance of fayalite and the emergence of wüstite(FeO). Furthermore, as the stages advanced, a three-layer structure comprising wüstite, magnetite(Fe3O4), and hematite(Fe2O3) was observed.
<Microstructure of blacksmithing slag(x100)>
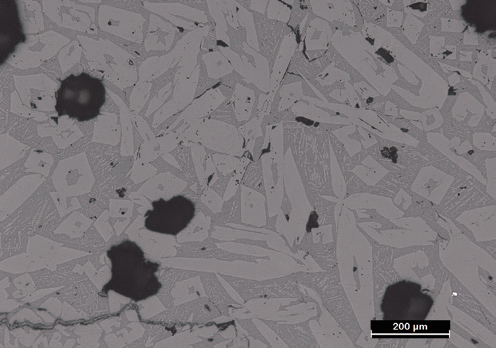
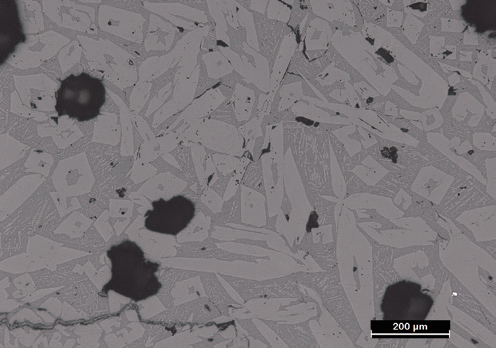
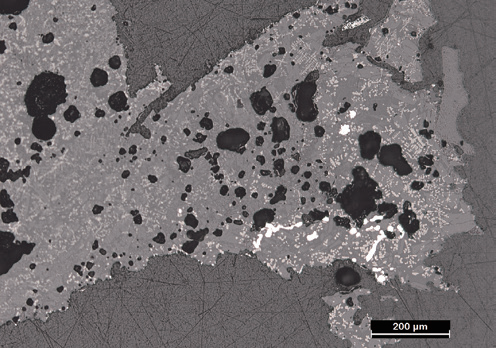
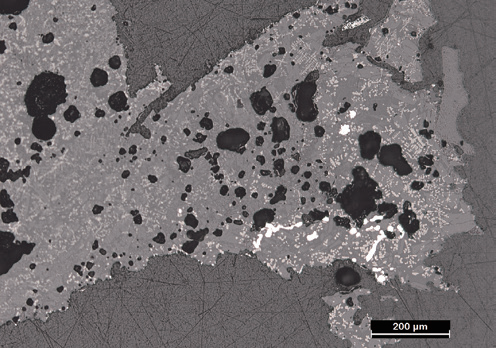
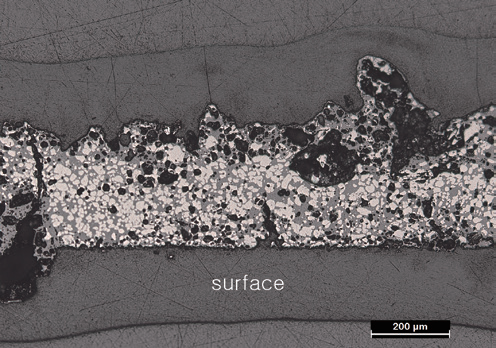
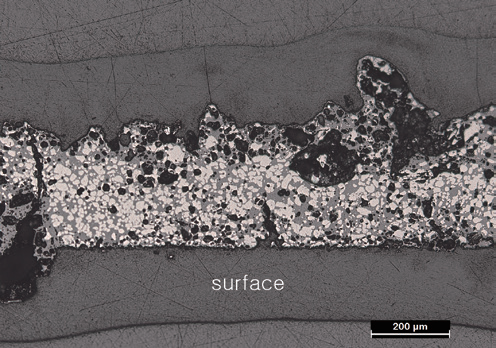
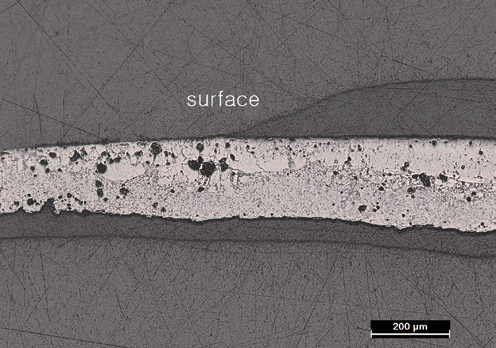
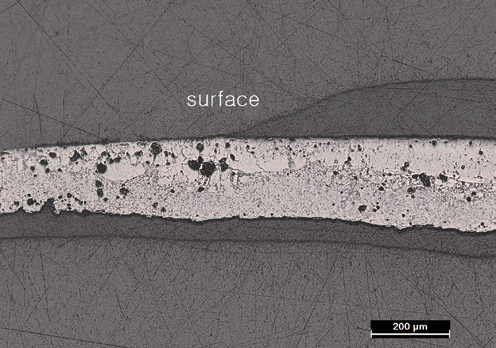
Major accomplishments
Replicating a Ring-Pommel Sword with Recreated Baekje Technology
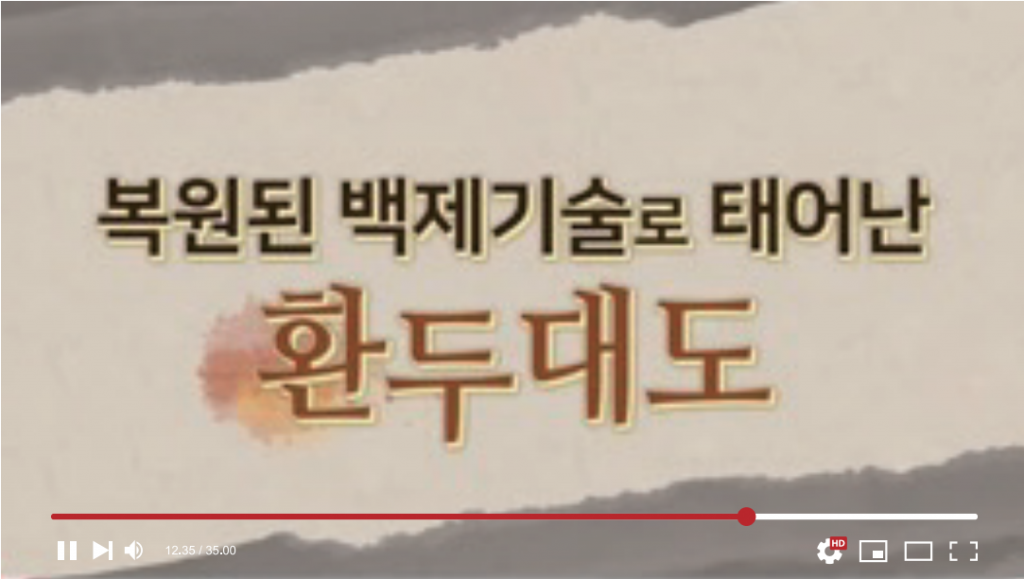
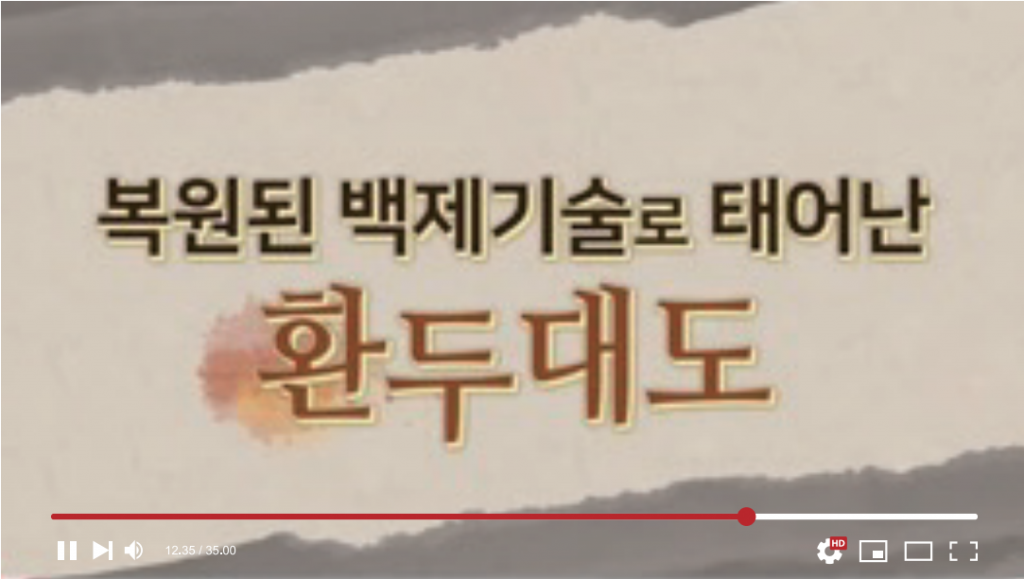
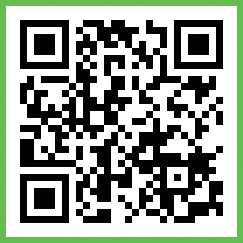
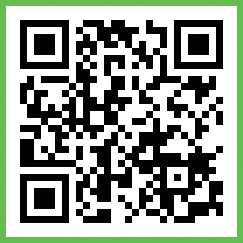
Study on the Production of Iron-bar through Restoration Experiments and Changes in Products by Process
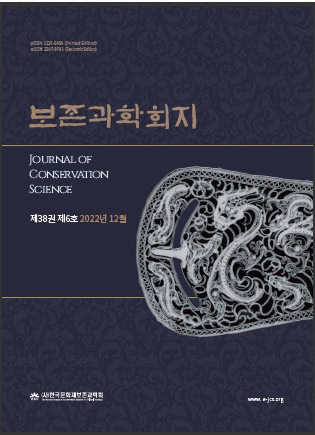
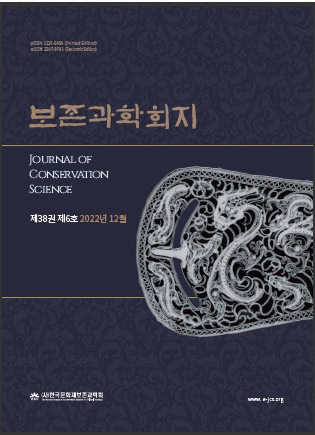
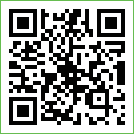
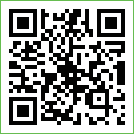
The ancient forging process seen through restoration experiments of iron Ingots and sword with ring pommel
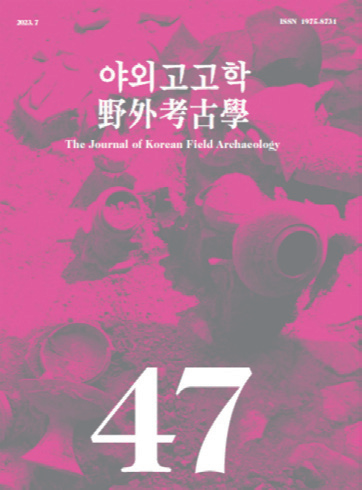
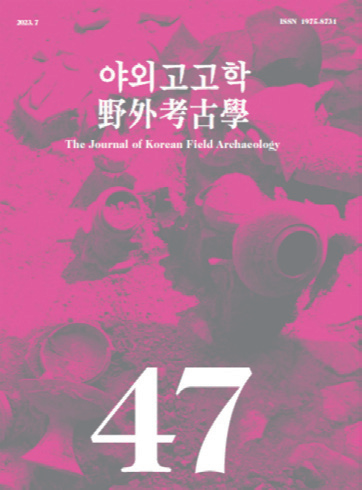
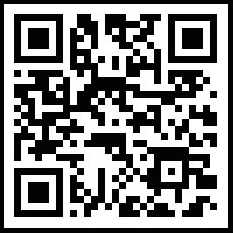
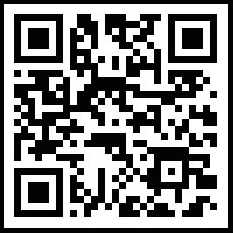